Vorort oder Inhouse Wartung:
Flexible Durchführung
Nach höchsten Standards:
Hersteller- u. Gesetzeskonform
Bereitstellung von Ersatzgeräten:
Vermietung von PSA
Termine immer im Blick:
Wir erinnern an Ihre Wartung
IHR PARTNER FÜR ARBEITSSCHUTZ & ARBEITSSICHERHEIT
Optimale Sicherheit aus einer Hand
Ihre Gesundheit und Sicherheit sowie die Ihrer Mitarbeiter stehen an erster Stelle. Mit gutem Grund unterliegen Atemschutzgeräte Pflege- und Wartungsvorgaben, die von der deutschen gesetzlichen Unfallversicherung (DGUV) und von Herstellern vorgeschrieben sind. Höchste Sorgfalt ist für die Sicherheit der Anwender und für einen zuverlässigen Betrieb der Geräte unerlässlich. Als herstellerunabhängiger Anbieter finden wir daher nicht nur die optimalen und auf Sie zugeschnittenen Produktlösungen, sondern stehen als kompetenter Partner auch bei der Produktwartung und bei Reparaturen an Ihrer Seite und sorgen dafür, dass Ihre Produkte jederzeit einwandfrei funktionieren. Unsere Servicemitarbeiter sind speziell ausgebildete und zertifizierte Servicekräfte und verfügen sowohl über das entsprechende Equipment und Service Software, um die Pflege und Wartung Ihrer Atemschutzausrüstung zu übernehmen. Als auch über die entsprechenden Autorisierungen der Hersteller, um für eine dauerhafte Sicherheit und Zuverlässigkeit der Technik zu sorgen. Sie führen den Service und die Wartung Ihrer Geräte gemäß Herstellerangaben und Vorgaben der deutschen gesetzlichen Unfallversicherung durch. Ob wiederkehrende Prüfungen von persönlicher Schutzausrüstung, deren Reinigung und Desinfektion oder die Befüllung von Atemluftflaschen – wir sind für Sie da.
Leistungen
Leistungen des
PM Service im Überblick
Der PM Service bietet umfassende Reparatur- und Wartungsarbeiten von Atemschutzgeräten sowie Arbeitsschutzequipment gemäß DGUV- und Herstellervorgaben an. Unsere zertifizierten Servicemitarbeiter verwenden Original-Ersatzteile und modernstes Prüfequipment. Unsere autorisierten Servicemitarbeiter führen die Wartungsarbeiten entweder direkt bei Ihnen vor Ort und zu Ihrem Wunschtermin durch oder Sie senden Ihre Ausrüstung in unsere Servicewerkstatt.
Unsere Servicemitarbeiter sind speziell ausgebildete und zertifizierte Servicemitarbeiter und verfügen sowohl über das entsprechende Equipment und Service Software, um die Pflege und Wartung Ihrer Atemschutzausrüstung zu übernehmen als auch über die entsprechenden Autorisierungen der Hersteller, um für eine dauerhafte Sicherheit und Zuverlässigkeit der Technik zu sorgen. Sie führen den Service und die Wartung Ihrer Geräte gemäß Herstellerangaben und Vorgaben der deutschen gesetzlichen Unfallversicherung durch.
Für den Fall das Sie während der Wartung ein Ersatzgerät benötigen, hält unser dort ansässiger Mietpool eine große Menge unterschiedlicher Geräte für Sie bereit. Diese sind neuwertig und werden regelmäßig nach jedem Einsatz umfassend gewartet.
Sobald wir Ihre Zusendung erhalten haben, prüft und erfasst unser Service Team Ihren Auftrag und sendet Ihnen einen Kostenvoranschlag bzw. eine Bestätigung zur Prüfung.
Die Durchführung der Arbeiten bieten unsere Servicepartner direkt bei Ihnen vor Ort, zu Ihrem Wunschtermin, an oder Sie schicken Ihre Ausrüstung bequem und einfach in die Servicewerkstatt.
Als besonderen Service übernehmen wir für Sie die komplette Termin-überwachung und -erinnerung, sodass Sie sich auf Ihr Kerngeschäft konzentrieren können und keinen Zeit- und Kostenaufwand für die Kontrolle der fälligen Wartungen aufbringen müssen. Sämtliche Geräte aller Kunden sind bei uns durch eine einmalige Seriennummer oder die durch uns angebrachten Barcodes datenmäßig erfasst. Anhand dieser Kennzeichnung können wir Verkaufsdatum, Garantiezeit sowie durchgeführte und anstehende Wartungen nachhalten. In regelmäßigen Abständen kontrollieren wir, welche Geräte planmäßig gewartet werden müssen und informieren Sie entsprechend über anstehende Termine.
Sie bekommen nach jeder Wartung ein Prüfbericht nach DGUV 112-190 und Herstellervorgaben und Ihre Produkte werden mit einer Prüfplakette versehen. Der Prüfplakette können Sie den nächsten Wartungstermin entnehmen. Die komplette Prüfdokumentation wird Ihnen transparent aufbereitet und zugeschickt. Die Dokumentation wird dabei bei jedem Service Termin fortlaufend weitergeführt, sodass Sie detaillierte Informationen über den Zustand Ihrer Produkte während der gesamten Einsatzzeit haben.
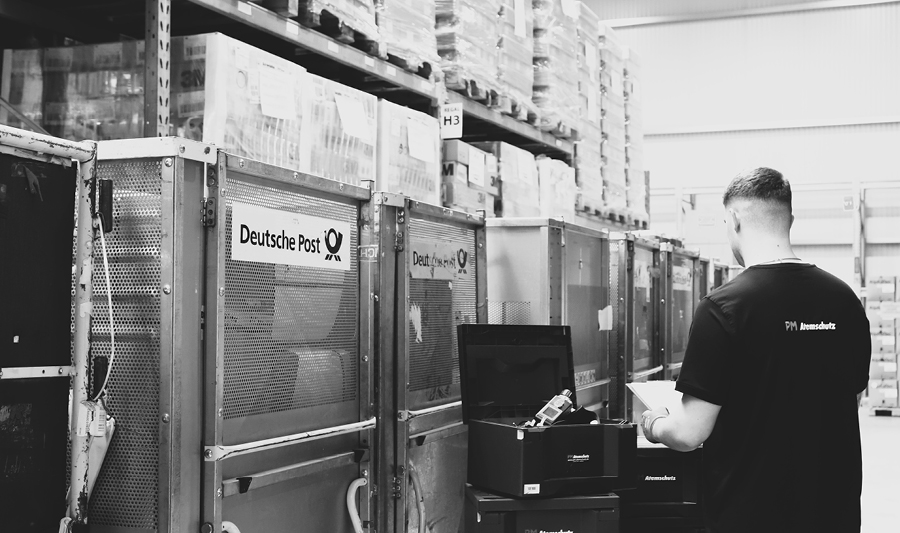
Wartung & Service
Ablauf Inhouse
In unserer Servicewerkstatt verfügen wir über modernstes Prüf- und Testequipment zur Prüfung und Wartung Ihrer persönlichen Schutzausrüstung. Sie können Ihre Geräte bequem zu uns einschicken, und unsere spezialisierten Techniker kümmern sich um eine schnelle und effiziente Wartung. Um eine minimale Ausfallzeit zu gewährleisten, halten wir stets eine ausreichende Menge an Ersatzteilen und Zubehör vorrätig.
Wartung & Service
Ablauf vor Ort
Als führendes Serviceunternehmen für Atemschutzgeräte bieten wir Ihnen einen erstklassigen vor Ort Wartungsservice an. Unsere spezialisierten Techniker kommen direkt zu Ihnen und sorgen für eine schnelle und effiziente Wartung – ohne lange Ausfallzeiten und aufwendigen Transport Ihrer Geräte.
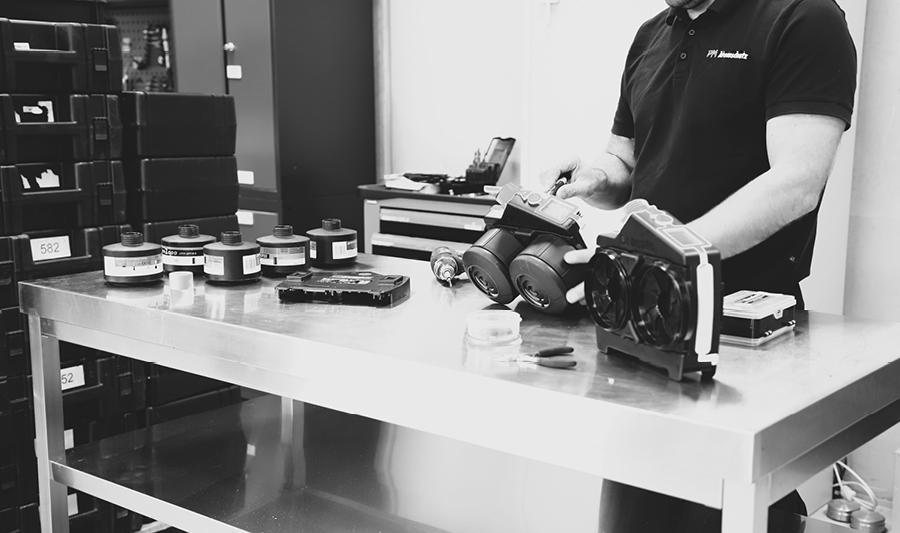
GEMEINSAM STÄRKER.
UNSERE PARTNER
Wichtige Information
Wartungs- und Reparaturarbeiten dürfen ausschließlich durch vom Hersteller autorisierte und zertifizierte Servicezentren durchgeführt werden. Die Zertifikate gelten nur für zugehörige Mitarbeiter der autorisierten Unternehmen, NICHT für Einzelpersonen und verlieren Ihre Gültigkeit mit Unternehmensaustritt. Mitarbeiter müssen regelmäßig geschult werden. Es dürfen nur Original-Ersatzteile verwendet werden. Eine Nichteinhaltung wirkt sich auf die Gültigkeit der Produktzertifizierung aus und damit auf die Gewährleistung und Haftung des Herstellers bei Arbeitsunfällen und Kontrollen. Bei Zuwiderhandlungen oder bei Durchführung der Wartung durch nicht zertifizierte Stellen/Personen erlischt die Herstellergarantie.
Wir sind Autorisierter und Zertifizierter Servicepartner folgender Marken:
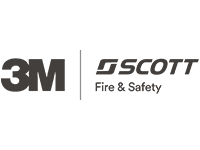

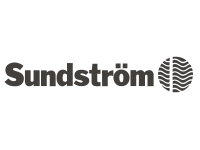
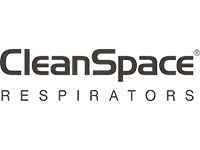
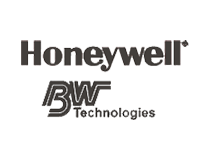
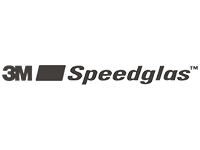
Weitere Hersteller, deren Serviceabwicklung wir Durchführen:
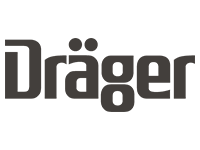
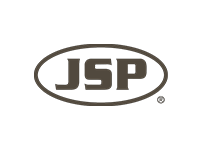
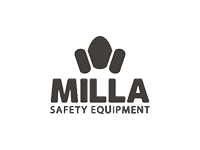

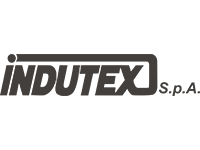
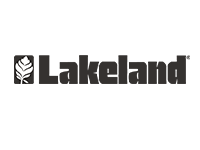
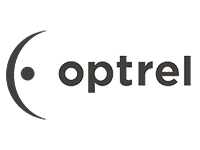
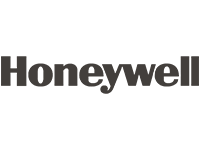
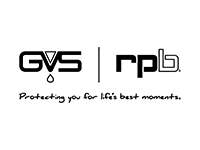
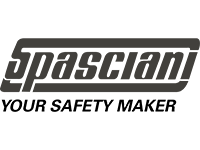
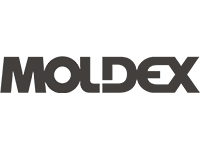
Leistungen
Wir reparieren und warten:
Wartung von Atemschutzgebläsen
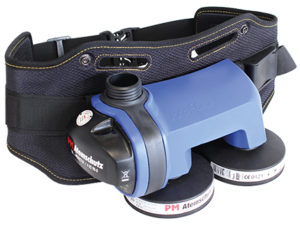
Wartung von Atemschutzkopfteilen
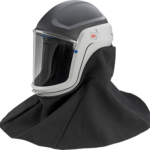
Wartung von Atemschutzhauben
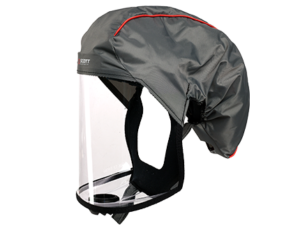
Wartung von Atemluftschläuchen
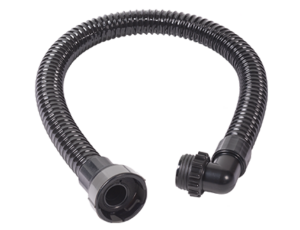
Wartung von Druckluft-Regelventilen
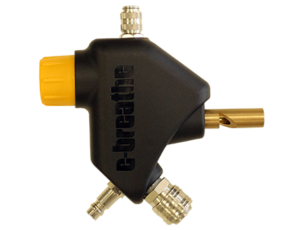
Wartung von Druckluft-Filterstationen
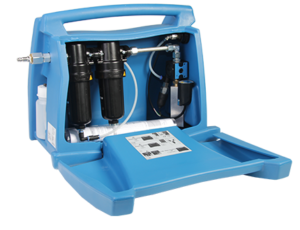
Wartung von Druckluft-Schläuchen
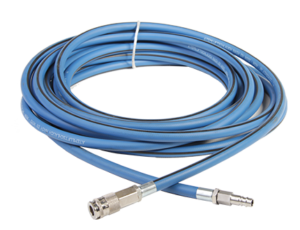
Wartung von Frischluft-Schlauchgeräten

Wartung von Vollmasken

Wartung von Halbmasken
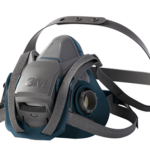
Wartung von Fluchtgeräten
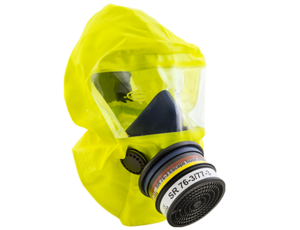
Wartung von Gasmessgeräten
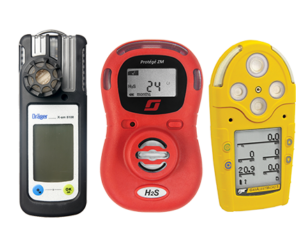
Wartung von Chemikalienanzügen
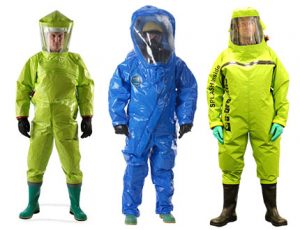
Wartung von Selbstrettern / Pressluftatmern
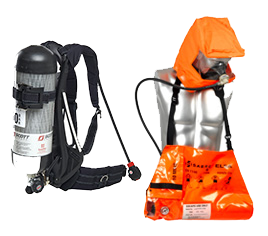
TÜV-Prüfung / Befüllung von Atemluftflaschen
Vorteile
Durch eine regelmäßige Wartung und regelmäßige Reparaturen ...
- Schützen Sie sich vor Ausfällen und verlängern die Lebensdauer Ihrer Geräte.
- Gewährleisten Sie die Funktionstüchtigkeit der Produkte und verlängern ihre Einsatzdauer.
- Erhalten Sie die höchste Schutzleistung für sich und Ihre Mitarbeiter.
- Erhöhen Sie die Herstellergarantie um bis zu 36 Monate.
- Bessere Absicherung im Unglücksfall: Nachweis der Einhaltung gesetzlicher Vorgaben durch regelmäßige Prüfdokumentation.
- Gewährleisten Sie die Einhaltung gesetzlicher Anforderungen: Gemäß §2 Abschnitt 4 der PSA Benutzerverordnung hat der Arbeitgeber durch Wartungs-, Reparatur- und Ersatzmaßnahmen, sowie durch ordnungsgemäße Lagerung dafür Sorge zu tragen, dass sich die persönlichen Schutzausrüstungen während der gesamten Benutzungsdauer funktionstüchtig und in einwandfreiem Zustand befinden.
WArtung
Ablauf Inhouse Wartung & Service
PM Inspektionsservice
So einfach funktioniert der PM Inspektionsservice!
1. Service Begleitschein
Bitte füllen Sie unseren Service-Begleitschein aus, damit uns direkt alle wichtigen Informationen und Daten zur Verfügung stehen und wir Ihre Anfrage schnellstmöglich bearbeiten können.
WICHTIG: Aufgrund gesetzlicher Vorschriften sowie zum Schutz der Mitarbeiter und der Umwelt benötigt wir zur Durchführung Ihres Auftrags diese unterschriebene Erklärung. Unser Service kann nur durchgeführt werden, wenn die Erklärung von qualifiziertem Fachpersonal korrekt und vollständig ausgefüllt vorliegt. Servicearbeiten können nur an gereinigten, desinfizierten und dekontaminierten Produkten durchgeführt werden.
3. Auftragserfassung & Kostenvoranschlag
Sobald wir Ihre Zusendung erhalten haben, prüft und erfasst unser Service Team Ihren Auftrag und sendet Ihnen einen Kostenvoranschlag bzw. eine Bestätigung zur Prüfung.
4. Auftragsbestätigung / -freigabe
Bitte senden Sie uns Ihre Auftragsfreigabe schnellstmöglich zurück, um eine schnelle Abwicklung Ihres Auftrages sicherstellen zu können.
5. Auftragsbearbeitung
Nachdem Sie uns Ihre Auftragsfreigabe übermittelt haben, wird Ihr Auftrag direkt an unsere kompetenten und erfahrenen Servicemitarbeiter übergeben.
2. Versand der Ausrüstung
Bitte packen Sie das/die zu wartende(n) Atemschutzsystem(e) (Gebläse, Akku, Gurt, Ladeschale, Schlauch, Kopfteil) in einen Karton oder, falls vorhanden, in unsere wiederverwendbare PM Service Box und legen Sie den ausgefüllten Servicebegleitschein dem Paket bei.
Versandanschrift:
PM Atemschutz GmbH, Im Abtsfeld 6, 41066 Mönchengladbach
6. Rücksendung der Ausrüstung & Rechnungserstellung
Die Rücksendung Ihrer Ausrüstung erfolgt schnellstmöglich. Sie erhalten von uns die komplette Prüfdokumentation inklusive Prüfbericht, sowie einen neuen Service-Begleitschein für Ihre nächste Wartung.
(Optional: Bei Bedarf senden wir Ihnen neue Verbrauchsmaterialien direkt mit. Bitte informieren Sie uns einfach im Vorfeld.)
WArtung
Ablauf vor Ort Wartung & Service
Als führendes Serviceunternehmen für Atemschutzgeräte bieten wir Ihnen einen erstklassigen vor Ort Wartungsservice an. Unser Ziel ist es, Ihre Atemschutzgeräte und das dazugehörige Zubehör in einwandfreiem Zustand zuhalten, um die Sicherheit und Gesundheit Ihrer Mitarbeiter zu gewährleisten. Unsere spezialisierten Techniker kommen direkt zu Ihnen und sorgen für eine schnelle und effiziente Wartung – ohne lange Ausfallzeiten und aufwendigen Transport Ihrer Geräte.
Voraussetzungen für eine optimale und reibungslose Wartung bei Ihnen Vorort:
Mitteilung über Wartungs- u. Reparaturumfang:
Bitte teilen Sie uns vorab die Anzahl der zu prüfenden Geräte sowie Gerätetyp und Hersteller mit. Sollten bereits bestehende Probleme oder Defekte an Ihrer Ausrüstung bekannt sein, teilen Sie uns diese bitte im Voraus mit. Dadurch können unsere Mitarbeiter die entsprechenden Ersatzteile direkt in entsprechender Anzahl vorhalten und sicherstellen, dass alle Reparaturen direkt vor Ort effizient und ohne Verzögerung durchgeführt werden können.
Zugang zu Ihrem Firmengelände und Wartungsbereichen:
Bitte melden Sie den Zugang unseres Mitarbeiters im Vorfeld in Ihrem Unternehmen/Werksgelände an. Teilen Sie uns zwingend im Vorfeld nötige Anmelde- oder Registrierungsprozesse mit, damit unser Personal ohne zeitliche Verzögerungen Zugang zum Gelände erhält. Wir behalten uns vor, entstandene Kosten für Registrierungen und Zeitverzug unseres anreisenden Personals gesondert in Rechnung zu stellen. Gewähren Sie unseren Technikern Zugang zu den benötigten Räumlichkeiten und stellen Sie sicher, dass alle relevanten Informationen und Dokumentationen zugänglich sind. Ein funktionierender Strom- und Wasseranschluss ist notwendig, um bestimmte Wartungsarbeiten durchführen zu können.
Bereitstellung der Geräte:
Stellen Sie sicher, dass alle Atemschutzgeräte und Zubehörteile gereinigt und zum Schutz unserer Mitarbeiter dekontaminiert (frei von Verunreinigungen durch biologische, chemische oder gesundheitsgefährdenden Stoffe) bereitliegen. Servicearbeiten können nur an gereinigten, desinfizierten und dekontaminierten Produkten durchgeführt werden.
Ansprechpartner vor Ort:
Ein Ansprechpartner sollte während der gesamten Wartungszeit für unsere Servicemitarbeiter zur Verfügung stehen, um Fragen zu klären und Abläufe zu koordinieren.
Details zu unserem Wartungsangebot
Wartung & Service
Unsere Servicekräfte sind ausgebildete Atemschutzwarte und werden bei jeder technischen Erneuerung am Gerät wiederholt geschult und unterwiesen, sodass sie ständig auf dem aktuellen Stand der Technik und der damit verbundenen Reparaturen sind.
Die von Ihnen eingeschickten oder von uns bei Ihnen vor Ort aufgesuchten Gebläse werden sorgfältig durch unsere Servicemitarbeiter inspiziert, auf kleinste Fehler hin geprüft und nötige Ersatzteile werden gewissenhaft gewechselt.
Anhand einer exakten Computeranalyse wird ein Atemschutzgebläse auf absolute Funktionstüchtigkeit hin überprüft. Die dafür entwickelte Software wertet alle Daten des angeschlossenen Gerätes aus und gibt mögliche Fehlermeldungen an.
Diese hat der Servicetechniker zu überprüfen und entscheidet anschließend welche Ersatzteile für die entsprechende Reparatur benötigt werden.
Sie erhalten von uns einen Kostenvoranschlag, anhand dessen Sie entscheiden können, ob das Gerät repariert oder entsorgt werden soll. Nach Ihrer Freigabe werden die nötigen Instandsetzungsmaßnahmen durchgeführt und Sie erhalten das einwandfreie Atemschutzgebläse mitsamt eines dokumentierten Wartungsberichtes zurück.
Sie bekommen automatisch zum nächsten Wartungstermin von uns Bescheid, sodass Sie sich keine Gedanken machen müssen, welches Gerät wann mit der nächsten Wartung fällig ist. Wir übernehmen für Sie die komplette Terminkontrolle.
Wartung & Service
Die Überprüfung der Dichtigkeit Ihrer Atemschutzvollmasken erfolgt in unserem Hause mithilfe des eigens für diesen Vorgang entwickelten PM-Tester USB RFID.
Durch das zuverlässige Dichtigkeitsprüfungssystem wird in einem Vorgang getestet, ob die zu prüfenden Vollmasken Ihren Ansprüchen in Sachen Sicherheit noch gerecht werden und Sie 100%ig schützen.
Sollte der Test nach wiederholtem Male scheitern, inspiziert unser Servicetechniker die Maske genau, um herauszufinden, welches Ersatzteil ausgetauscht werden muss damit eine zuverlässige Dichtigkeit gewährleistet wird. Anschließend erhalten Sie einen Kostenvoranschlag über die Reparatur, welche erst nach Ihrer Freigabe durchgeführt wird.
Die Maske wird nach der Reparatur gereinigt, desinfiziert sowie in Folie eingeschweißt und mit einem Wartungsbericht versehen schnellstmöglich an Sie zurückgeschickt.
Wartung & Service
Die Firma PM Atemschutz bietet Ihnen die Möglichkeit, Ihre Chemie- und/oder Brandfluchthauben des Herstellers Sundström zu warten.
Bei den Brandfluchthauben SR 77 mit oder ohne Tasche wird bei der fälligen Wartung ein komplettes Service-Kit ausgetauscht. Dieses besteht aus dem Filterwechsel des ABEK1-Co-P3 Filter, den Ersatz und das Einschweißen in einen neuen Alu-Beutel sowie den Tausch des Filterrings, des Visierschutzes, des Antibeschlagtuches, der Labels sowie der Gebrauchsanweisung.
Dieses besteht aus dem Filterwechsel des ABEK1-Co-P3 Filter, den Ersatz und das Einschweißen in einen neuen Alu-Beutel sowie den Tausch des Filterrings, des Visierschutzes, des Antibeschlagtuches, der Labels sowie der Gebrauchsanweisung.
Wartung & Service
Die PM Atemschutz GmbH bietet eine breite Vielfalt an Gasmessgeräten der Firma BW Technologies und Scott Safety an. Hier findet sich für nahezu jedes Gas und jeden gefährdeten Arbeitsplatz das passende Warngerät, um Sie rechtzeitig über hohe Konzentrationen gesundheitsgefährdender Gase und Dämpfe in Kenntnis zu setzen.
Bei den Gasmessgeräten erstreckt sich unser Service von der Kalibrierung, über Überprüfung und Reinigung bis hin zum Sensortausch. Zu unterscheiden ist hierbei zwischen Kalibrierungsvorgängen von:
1-Gas Messgeräten
2-4-Gas Messgeräten und
5-Gas Messgeräten
Die Kalibrierungen können bei Ihnen vor Ort oder in unserer Werkstatt erfolgen. Nach jeder erfolgreichen Kalibrierung erhalten Sie als Beleg ein Konfigurations- und ein Kalibrierzertifikat.
Sollte Ihr Gerät einmal defekt sein, bieten wir Ihnen selbstverständlich die Möglichkeit, das Gerät zu überprüfen und es soweit möglich in Stand zu setzen. Sollten wir einmal nicht über die technische Ausrüstung die eine Reparatur erfordert verfügen, schicken wir das Gasmessgerät für Sie zum Hersteller. Nach Erhalt eines Kostenvoranschlages haben Sie die Option zu entscheiden, ob die Reparatur durchgeführt werden soll oder nicht.
Selbstverständlich besteht für die Geräte die gesetzliche Garantie von 24 Monaten. Bei den Sensoren kann die Garantiezeit je nach Ausführung abweichen. Dies ist im Vorfeld bei uns zu erfragen.
Wartung & Service
Selbstretter
Wir übernehmen die Prüfung Ihrer Selbstretter wie z.B. Elsa-Dash auf Ihren Wunsch oder zum regulären Wartungsintervall. Dabei wird zwischen Funktionsüberprüfung mit und ohne Reinigung und Desinfektion nach Gebrauch unterschieden.
Darüber hinaus sind generelle Wartungsintervalle von den Herstellern vorgegeben, die unbedingt zu beachten sind. Diese wären:
1-Jahres Service
Überprüfung zzgl. gemäß Herstellerangaben benötigte Ersatzteile (1 x Sinterfilter)
3-Jahres Service
Überprüfung zzgl. gemäß Herstellerangaben benötigte Ersatzteile (1 x O-Ring, 1 x Sinterfilter)
6-Jahres Grundüberholung
Überprüfung zzgl. gemäß Hersteller benötigte Ersatzteile je nach Geräteausführung (mit Tasche oder Weste, Elsa Sprint mit Vollmaske oder Haube)
Pressluftatmer
Die Überprüfung von Pressluftatmern erstreckt sich ebenfalls von der reinen Funktionsüberprüfung inkl. Check des Lungenautomaten, über Reinigung und Desinfektion nach Gebrauch, bis hin zur 1- und 6-Jahres Grundüberholung, bei denen auch Ersatzteile gemäß den Herstellerangaben gewechselt werden müssen.
Wartung & Service
Nach §15 (7) der Betriebssicherheitsverordnung müssen Atemschutzgeräte alle 5 Jahre TÜV- geprüft werden und dürfen somit nicht eingesetzt werden, sollte diese Frist laut Prüfetikett überschritten sein.
Wir haben die Möglichkeit Ihre Atemluftflaschen (bis 10l oder CFK-Flaschen) zur TÜV-Prüfung vorzulegen. Alles, was Sie tun müssen, ist uns Ihre entleerten Atemluftflaschen frei Haus zukommen zu lassen und den Rückerhalt abzuwarten.
Befüllung von Atemluftflaschen (bis 4l oder bis 10l Inhalt)
Das neue Befüllen mit Atemluft nach DIN EN 12021 nach der TÜV-Prüfung oder das generelle Füllen sollte Ihre Flasche verwendet und leer geworden sein können wir selbstverständlich auch für Sie übernehmen.
Für den Transport der Atemluftflaschen gelten gefahrgut- und transportrechtlichen Regeln und Vorschriften.Preise für die TÜV-Prüfung, das Befüllen und den Transport gefüllter Atemluftflaschen erhalten Sie selbstverständlich auf Anfrage.
Sie haben fragen zu unserem service und wartungsangebot? Kontaktieren sie uns:
Kontaktformular
Unsere Geschäftszeiten:
Mo. – Do. 08.00 – 16.30 Uhr
Fr. 08.00 – 14.30 Uhr
PM Atemschutz GmbH
Im Abtsfeld 6
41066 Mönchengladbach
Deutschland